It’s been a while without updates, reason being that a new project dropped in my shop two weeks ago: a new electric motorbike to work on!
Got it for free, so that’s a pretty nice deal. Most of it is toast, but the important stuff is still there and can be reused: the frame, the suspension, the front fork, the brakes and the electric motor are all good. All the rest is either gone or crappy, so I’ll replace the entire wiring harness, the battery, throw away all the plastics, the lead acid batteries, the motor controller, etc.
Anyway, as some of you guys know I already have an other electric motorbike (the black one you can see on previous pic), so my plan for this new one will be to make something a little bit weird and crazy looking. Basically the idea is to strip absolutely everything I can down to the absolutely necessary stuff. I spent some time 3D modelling everything to get a better idea of the final results, and hopefully if everything goes as planned, it should resemble something like this:
It’s a bit weird, I know, it will likely be uncomfortable, I know that too, but I quite like it and I’d like to give it a try and see if it actually works in real life. And I can always redo it differently if it turns out to be crap later.
Anyway, I started to build the thing, stripped down the frame, made some cuts, tack welded some tubes, ordered and received a new battery…
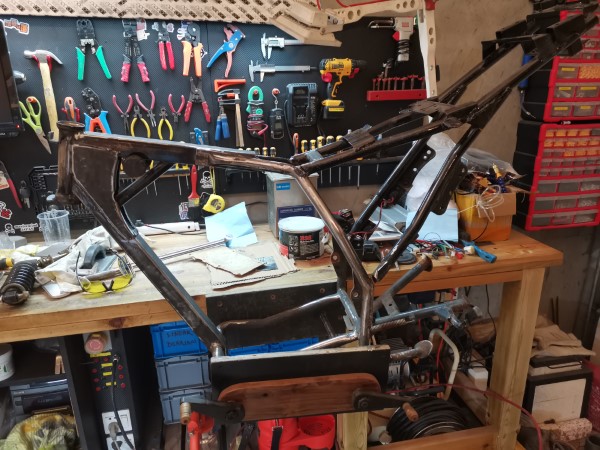
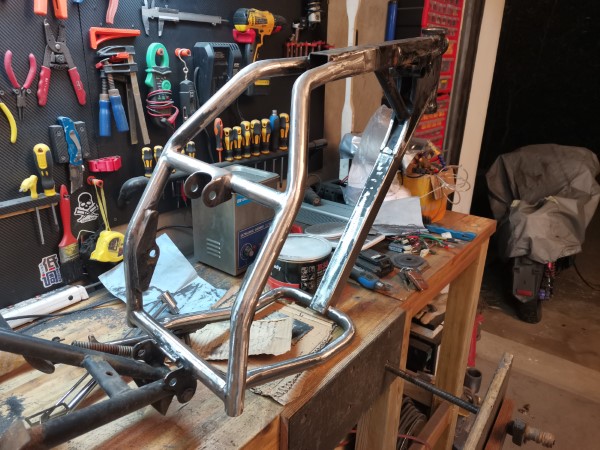
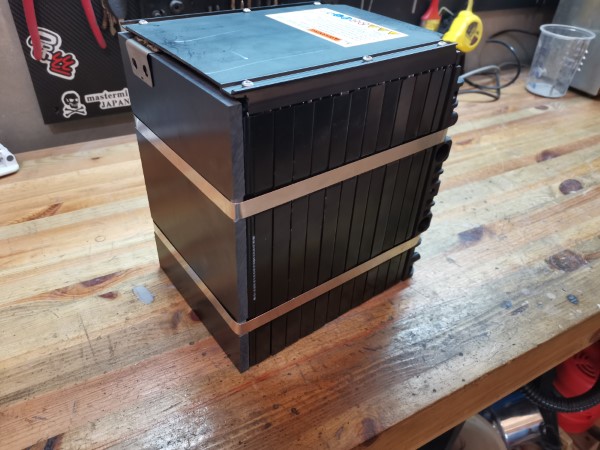
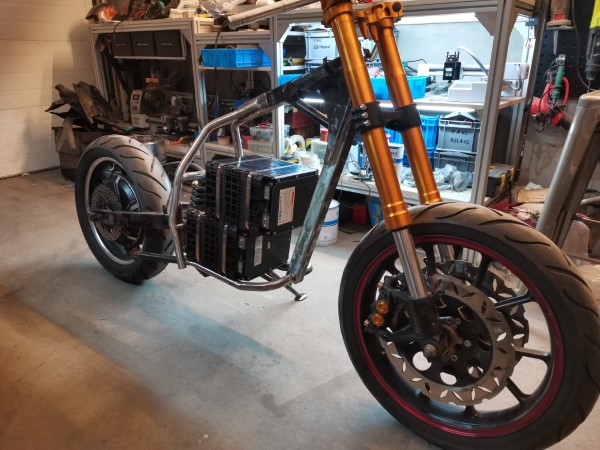
The BOx will be a very important tool for this build, I’ll use it to print mockups to decide on the final parts shapes, to print some molds in order to make a proper carbon fiber job later, to print some plugs I will use to make aluminum castings and also to print some parts that will remain on the bike.
The two parts of the saddle as well as the little black connectors at the end of the tubes were 3D printed with the BOx. In the final version the connectors will be aluminum cast and the tubes will be carbon fiber. Also carbon fiber for the bottom part of the saddle and I plan to try making the top out of silicone covered with leather. Not sure if this is gonna work, usually people use foam so I wonder if there is a reason why silicone isn’t used there except for the fact that it is a little bit more expensive?
Currently printing a slightly wider version of the saddle that will be relocated a bit more towards the front. The printer works amazingly well so far, I just hit print and go do something else, I never had a first layer fail and basically every print I’ve done since I replaced my motherboard was a success. I now have enough confidence to let it run during the night, only issue I had was that the filament sensor didn’t work for some reason I need to investigate, probably some wrong configuration in my firmware, no biggie.
The only thing I need to work on is to make filament change easier, it is quite a pain to change it since there is still lots of resistance in the bowden tube. This is quite important since this printer is very hungry for filament, I can use a spool in less than a day, it is really fast.
Anyway, it should be a nice and fun project and my new printer will play a central role in it !
If some of you guys want to follow the build I’ll post updates here on the endelss-sphere forums: https://endless-sphere.com/forums/viewtopic.php?f=12&t=109246&sid=a06e8a104e42351d58649903a7a4575a