Client just picked up the piece, and was very happy with it. So that’s a good thing!
Things I learned…
Make sure to understand the client’s project before pricing. Having to buy new SS legs ate up most of my profits from the piece. On the other hand, the flexibility of the MPCNC design made it easy to transition! And now I’ve got the hardware to handle it in the future.
Air assist rocks. In the picture below, the “&” was burned without the air assist, and the “J” was burned with the air assist.
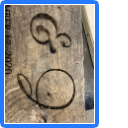
Failing the air assist option (for whatever reason), 3M low tack tape works surprisingly well for removing smoke marks from irregular surfaces. Because of the weathered surface, sanding was NOT an option. So while I was waiting for the last part to finish burning, I was noodling how to clean up the smoke. So I tried the tape I had picked up for paint masking. Here’s the “before” tape cleanup, and you can see how smoked the cross-stroke of the “t” was.
And in this picture, after I had gone over the smoke with the tape:
Another lesson… When things go south on you, having a repeatable starting point is essential! And don’t panic! About midnight last night, my machine just stopped moving at about 3/4 the way through the job. The last line etched was about 3mm above the cross-stroke of the “t”. And about then, I just felt sick. So I ended up making a copy of the Lightburn file, then removing all the nodes of the text below that point (because I really didn’t want to burn the whole thing over). I then used the registration marks on the 2x4’s to line things up, along with the “Position Laser” menu option in Lightburn to make sure that when I started the job, it was going to burn at the correct point.
For some reason, I ended up having to manually re-position the beam for each of the three sections I had to do (the top of the “P”, the top of the “t”, and the top of the “&”) separately. When it was done, I couldn’t tell where the job restarted. In the pic below, the restart was somewhere between the two sections that had missed steps (surprisingly enough)…
The first missed step happened before the job failed; I think my control board or drivers overheated after 5 hours. The second missed step I have no idea why it happened, but at that point, I was watching the job like a hawk, and as soon as I noticed it was out of alignment, I whacked the beam over the 2 mm it needed to be back in sync with the job. What a fricking nightmare at 2 am!
So then this morning, I used the same technique to burn the “Jayson” on the beam, as my MPCNC wasn’t big enough to handle the entire width. Had the air assist on from the start this time, and it burned beautifully without any issues. No missed steps, no smoke issues, nothing.
Anywhoo… Anyone finishing reading this saga deserves a cookie. Or beer. Or something. Here’s the end result. Hoping to get a pic of it in place.
And for the record, this was the sample board the client gave me, and the test burn I did on it. No laser required, and it just burned beautifully on the surface. The actual beam was a nightmare. That would be another lesson learned… When asking for a sample to do a test burn, make SURE it’s from the same piece of wood. But even the beam didn’t burn consistently from one area to another.
Clint